Structural insulating panel production line Avangard-LSP-4
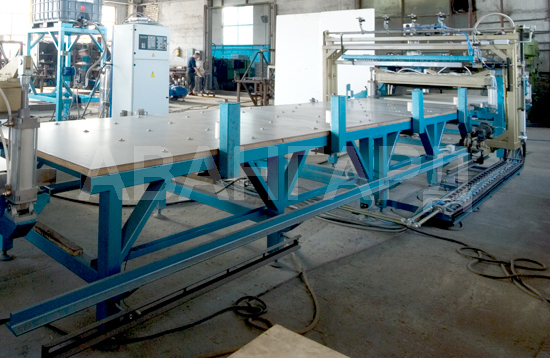
Line for the production of structural thermal insulation panels, SIP panels. The line is manufactured by the Avangard machine tool company. Favorable delivery terms, reasonable price.
AvangardLSP-4Video Avangard-LSP-4 structural insulating panel production line
Video of the line for the production of SIP panels Avangard-LSP-4.
2018-11-07T16:19:27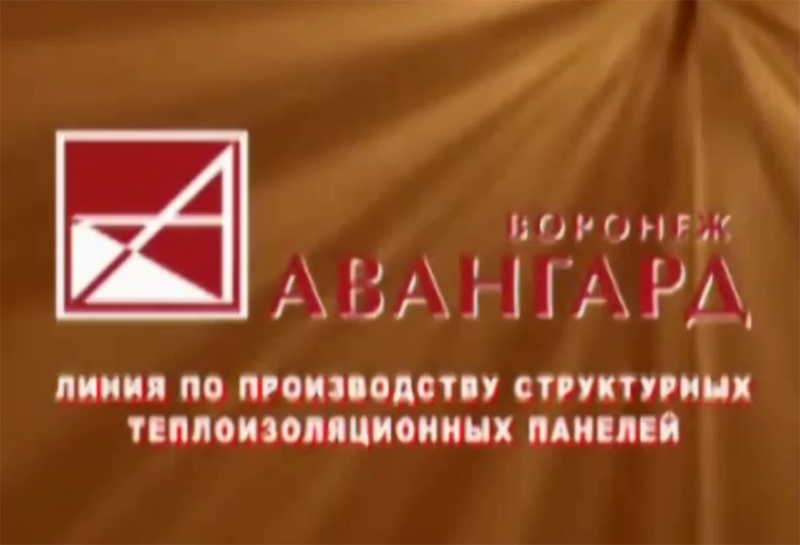
The Avangard - LSP line for production of structural insulating panels (SIP) is designed for production of sandwich panels based on OSB and expanded polystyrene. SIP sandwich panel is a monolithic structure obtained by gluing two OSB 3 plates and expanded polystyrene, used as heat and sound insulation material, by pressure.
The line is equipped with an automatic glue-bearing head with software control.
The line is manufactured in three modifications: Avangard-LSP-4, Avangard-LSP-2 and Avangard-LSP-1.
THE LINE OPERATION
Two oriented strand boards (OSB) are put on the assembly table, placed according to the limit stops and fixed with eccentric clamps.
A command to apply the glue is generated from a stationary or remote control panel. At the same time, a container with sealing liquid is put down on the glue application head, and the head moves along the guide rails to the beginning of the glue application area. The glue feed is activated, and the head, while moving along the guides, applies thin strips of glue on the OSB surface with a step of 12.5 mm. At the end of the glue application area, the head automatically stops, the container with sealing liquid rises and closes the outlets of the glue distribution bar from contact with air. The head begins to move in the opposite direction; the water supply is turned on, water is sprayed on the surface of the plates through the nozzles, being a hardener for the glue.
After placing the EPS foam on the plates, the processes of glue application and water supply are repeated. Then the OSB plate is placed on the foam and the assembled sandwich panels are moved to the pressing area by a conveyor.
Each press is equipped with six air bags which provide a force of 17 tons at an air pressure of 5 atm, and evenly distribute it over the entire surface of the sandwich panel. After leaving it under the press for about 10 minutes, the finished panel is fed by a conveyor to the receiving table, from which it is put manually or by means of lifting mechanisms with pneumatic pumps into storage in the workshop.
Further on, the assembly, pressing and unloading processes are carried out simultaneously.
Technical specifications of the Avangard-LSP-4 line for production of sip panels
Parameter | Value |
---|---|
Automatic glue application unit | 1 |
Assembly table, pcs | 2 |
Pneumatic press | 4 |
Table for the finished products output | 2 |
Stand for container with glue | 1 |
Productive capacity, pcs per shift | up to 320 |
Overall dimensions of the line: | |
width, m | 2,30 |
length, m | 26,10 |
height, m | 1,95 |
Overall dimensions of the manufactured panels: | |
width, mm | 1250 |
length, mm | 2500-3000 |
height, mm | 100-230 |
Weight, kg | 5500 |
Electric motor power, kW | 8 |
Power supply voltage, V | 380 |
Type of current | three-phase alternating |
Current frequency, Hz | 50 |
In the summary table, you can compare the technical characteristics of SIP panel production lines.